Exploring the Applications of Plastic Injection Molding Across Industries
Plastic shot molding stands as a cornerstone of modern-day manufacturing, supplying amazing versatility across varied industries such as auto, consumer items, healthcare, and electronic devices. Understanding exactly how these advancements influence the landscape of production can reveal much regarding future patterns and techniques.
Automotive Market Innovations
Changing the automotive landscape, plastic injection molding has actually arised as a vital technology in the production of ingenious vehicle components. This production procedure allows for the development of intricate geometries and lightweight parts, substantially adding to lorry performance and performance.
In modern vehicle layout, plastic injection molding helps with the manufacturing of parts such as bumpers, control panels, and interior trim pieces. These components not only improve visual allure yet also improve security and performance. The capacity to mold and mildew detailed layouts makes it possible for the assimilation of innovative attributes like air bag systems and digital user interfaces straight into the structural components.
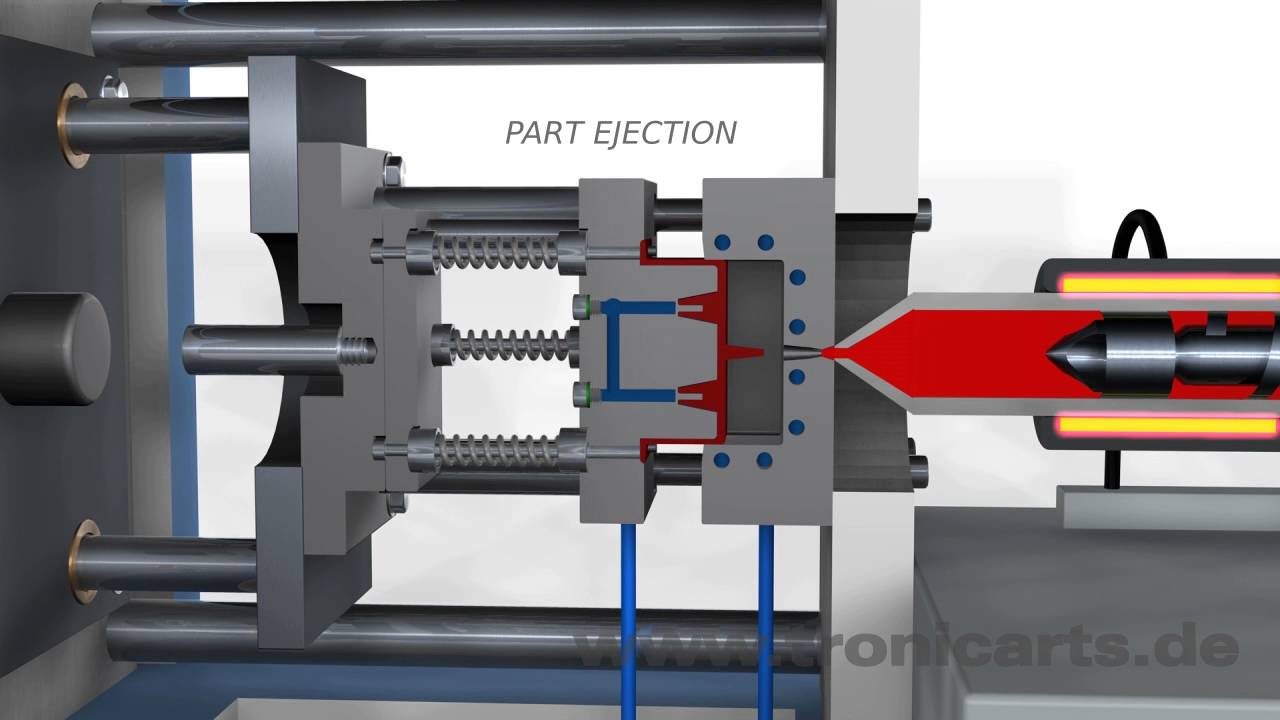
As the automotive sector remains to accept electrical and autonomous innovations, the duty of plastic injection molding will come to be increasingly crucial. Its flexibility and efficiency setting it as a keystone modern technology for future developments in lorry design and production, driving innovations toward a much more lasting auto community.
Durable Goods Production
The impact of plastic injection molding prolongs past the auto sector, considerably influencing durable goods making. This versatile technique enables the production of a broad variety of items, varying from family things to detailed digital components. The ability to create complex shapes and designs with high precision allows manufacturers to meet consumer demands for both functionality and aesthetic appeals.
Among the main advantages of plastic injection molding in consumer goods is its efficiency. The process enables high-volume manufacturing, lowering production prices and preparation. This effectiveness is important in a market defined by quickly changing consumer choices and trends.
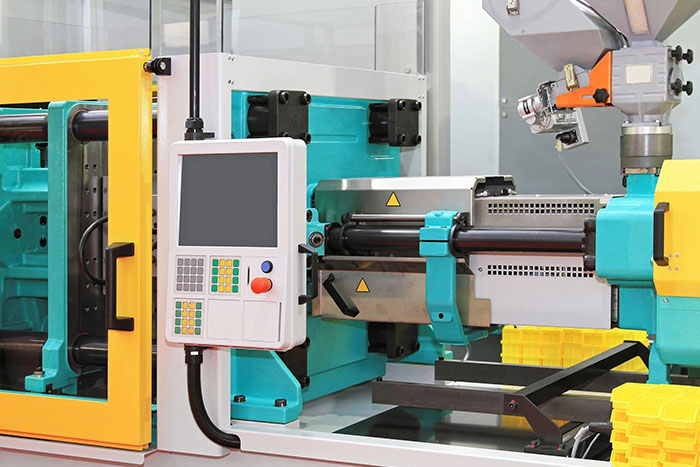
Eventually, plastic injection molding works as a cornerstone in consumer products making, enabling the production of diverse, top notch items that deal with developing market demands while optimizing operational effectiveness. This versatility guarantees its ongoing importance in the competitive landscape of customer items.
Medical Care Applications
In the medical care field, plastic injection molding plays an important function in the manufacturing of a variety of medical devices and components. This manufacturing method allows the development of specific and intricate shapes needed for various applications, from surgical tools to analysis equipment.
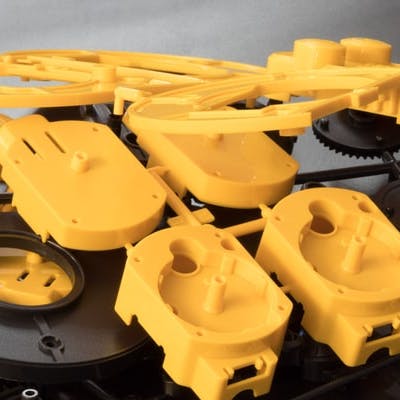
Additionally, plastic shot molding permits the assimilation of features such as texturing and complicated geometries, which can improve the functionality and individual experience of medical gadgets. The procedure also supports quick prototyping and brief preparations, making it possible for producers to react promptly to market needs and technical innovations.
Electronics Manufacturing Strategies
As sectors increasingly depend on sophisticated production procedures, plastic shot molding has actually also found considerable applications within electronics production. This method allows for the effective development of detailed parts that are essential for modern electronic tools. From smartphone cases to motherboard, the accuracy and versatility of shot molding assist in the production of top quality parts that meet rigorous industry requirements.
One of the vital advantages of plastic injection molding in electronics is its ability to generate complex geometries that would be testing to attain with typical production techniques. The fast cycle times connected with the process additionally boost manufacturing effectiveness, enabling manufacturers to respond promptly to market demands.
Furthermore, the use of specialized thermoplastics can improve the efficiency of digital components. Products such as polycarbonate and abdominal muscle use high sturdiness and outstanding electrical insulation, making them excellent for applications varying from connectors to real estate redirected here rooms.
Additionally, shot molding supports the integration of numerous functions right into single components, lowering assembly time and prices. As innovation continues to breakthrough, the function of plastic shot molding in electronics manufacturing is likely to increase, driving advancement and enhancing item performance throughout the industry.
Sustainability in Shot Molding
Sustainably incorporating methods in injection molding progressively shapes the future of production, attending to growing ecological concerns. As markets pursue eco-friendliness, the shot molding procedure adapts by executing energy-efficient technologies and sustainable products. Eco-friendly and recycled plastics are acquiring traction, lowering dependence on fossil gas and reducing waste.
Additionally, innovations in equipment and strategies aim to lower power intake during production. For example, electrical injection molding devices are coming to be more common, using substantial reductions in energy usage compared visit to standard hydraulic systems. These devices not only save energy however additionally boost accuracy and reduce cycle times, leading to lower operational costs.
Furthermore, companies are embracing closed-loop systems to handle waste efficiently. By recycling scrap material produced during the manufacturing process, they can minimize environmental impact and advertise source performance (Plastic Injection Molding). Applying lasting methods in injection molding not only meets regulatory requirements yet additionally deals with the boosting customer demand for ecologically accountable products
Conclusion
In verdict, plastic injection molding offers as a vital production procedure throughout numerous industries, consisting of automotive, customer items, health care, and electronic devices. Thus, plastic injection molding continues to be important for fulfilling the dynamic demands of contemporary markets while advertising sustainable manufacturing techniques.
Plastic shot molding stands as a cornerstone of contemporary production, offering amazing convenience across diverse markets such as auto, consumer goods, health care, and electronic devices.In modern-day automotive design, plastic injection molding assists in the manufacturing of parts such as bumpers, dashboards, and interior trim pieces.As markets progressively rely on innovative manufacturing processes, plastic injection molding has also found considerable applications within electronics production.In verdict, plastic injection molding serves as a crucial production procedure throughout different markets, consisting of vehicle, customer products, view it now healthcare, and electronics. Therefore, plastic injection molding remains vital for satisfying the dynamic needs of modern-day markets while advertising lasting production methods.